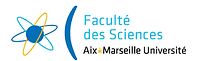
Nanomaterials by sol-gel processes
Sol-gel has emerged in the late 20th century as an alternative soft method to produce ceramic materials from inorganic molecular precursors without going through a drastic thermal treatment step. Later it was revealed that it does not only apply to silica materials but also to almost all other types of metal oxides and some non-oxides. Today it is a growing alternative green chemistry with a market of 2 billions euros and a compound annual growing rate of 8%. Amongst these, sol-gel coatings cover above 90% of the latter market and touch many industrial and technological domains from applied biomedical to quantum physics. Sol-gel is particularly well-adapted to thin-film processing as a result of the possibility to perfectly tune and control the rheology of the initial chemical solution to allow for perfect shaping of the materials prior to solidification. In sol-gel thin film processing, precursors and other solutes can be of different natures and forms, but have to be dissolved or suspended in the liquid. The film is formed through evaporation-induced consolidation of the homogeneous wet layer after deposition, but is often completed by an additional treatment (thermal, chemical…). The method is very flexible and allows (i) complex chemical deposition, (ii) multilayer processing, (iii) porosity control, and (iv) lateral and in depth gradients generation.
Liquid deposition processes are very versatile methods to produce highly homogeneous coatings, with controlled thickness typically ranging from few nanometers to few micrometers, through the spreading of a solution onto a substrate and evaporation of volatile compounds. They are seen as serious alternatives to dry deposition techniques, such as PVD, CVD or PECVD, because they combine excellent control of the inner layer structure and composition with rapidity and low cost. Amongst the various available techniques, some are already commonly used in various R&D and production industries, such as dip coating or spin coating, while others are still in their infancy and are in the process of being better understood and mastered, such as spray coating. For a better understanding, all available liquid deposition techniques are usually described by a sequence of identical successive steps: (i) the initial chemical solution formulation, (ii) the solution spreading on the surface of the substrate, (iii) the evaporation of the liquid solution layer, (iv) the layer post processing, and finally (v) the layer final treatment for stabilisation. These steps can all be individually addressed because they are separated in time, except for steps (ii) and (iii) since they are intimately linked in the space-time dimension of the processing. However, because controlling both the solution spreading and evaporation simultaneously is extremely difficult, one needs to be able to select the best conditions in which viscous flow dynamics and evaporation can be separately addressed.
Processing coatings from sol-gel
Sol-gel chemistry
